Publié sur Watchonista.com, le réseau social de l'horlogerie
La gangrène de la contrefaçon n’est pas une maladie récente. Elle infectait déjà l’horlogerie au XVIIIème siècle. Pour se prémunir contre l’usurpation de la déjà prestigieuse appellation Genevoise, la corporation d’horlogers de l’époque créa le Poinçon de Genève.
Comme le droit commercial de l’époque était plutôt inexistant, les dirigeants de l’horlogerie Genevoise d’alors ont opté pour le saut qualitatif, afin de se différencier. Le Poinçon de Genève était né. Ses critères de qualité étaient suffisamment difficiles à remplir pour permettre de différencier une vulgaire contrefaçon d’une montre fabriquée sur le canton et selon les critères du Poinçon.
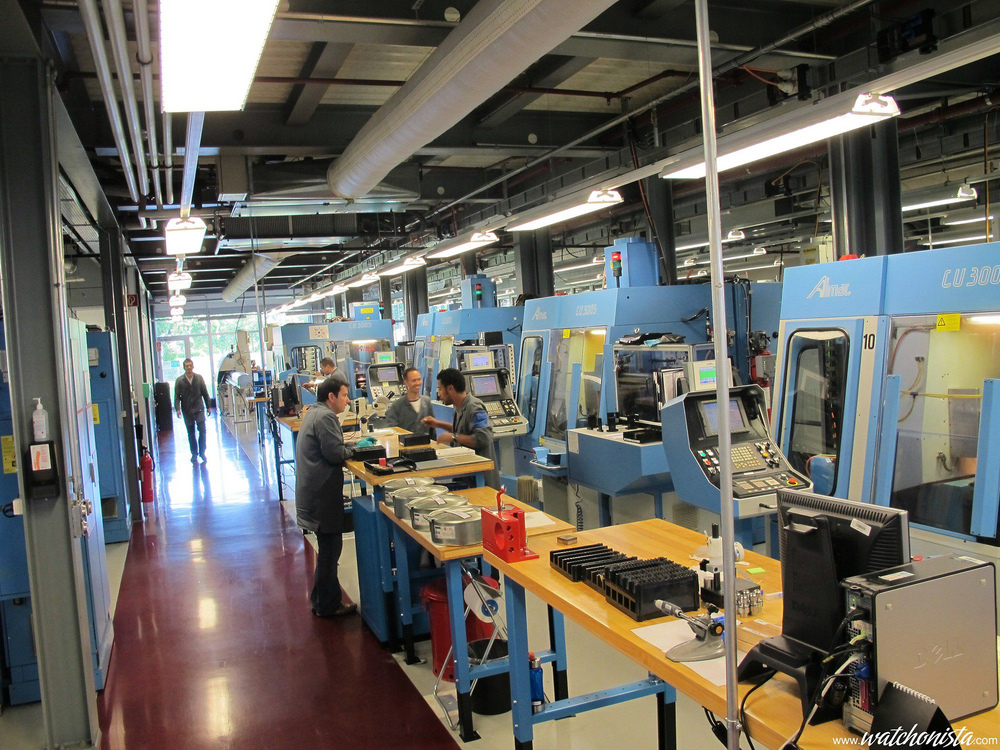
Ces critères ont été étendus en 2011 à l’intégralité de la montre. Le Poinçon est difficile à obtenir, car il impacte majoritairement les parties non-visibles d’une montre. Cela signifie qu’il faut investir beaucoup d’énergie pour finir des éléments que seul un horloger sera en mesure d’admirer, par exemple lors d’un service.
Le Poinçon concerne principalement la finition: l’intégralité des composants ne doit comporter aucune trace de découpe, ils doivent tous subir une finition telle que perlage, étirage, et surtout polissage. Ce travail garantit également une meilleure durabilité des composants.
Si l’esthétique est essentielle, à présent le Poinçon de Genève comporte aussi quatre critères de performance : l’étanchéité, la précision, les fonctions proposées, ainsi que la réserve de marche testée dans des conditions reproduisant au plus proche, celles dans lesquelles les garde-temps sont portés par les clients. Les tests de précision chronométrique s’effectuent par comparaison photographique sur un cycle de sept jours. L’écart constaté doit être inférieur à une minute sur la période.
En 2011, l’industrie des montres Suisses a produit 29,8 millions de pièces. Seul un million a été certifié par le COSC (par Timelab, qui gère aussi le Poinçon) et 25.000 par le Poinçon de Genève. Sur ces 25.000 montres, 5000 sont produites par Roger Dubuis, soit l’intégralité de la production de la marque.
La Manufacture Roger Dubuis est donc dans une situation unique à plusieurs titres.
La plupart des manufactures du Canton de Genève se situent sur les sites horlo-industriels de Meyrin ou de Plan-Les-Ouates. La quasi-totalité de ces manufactures disposent d'un ou plusieurs sites, souvent situés dans la Vallée de Joux où à la Chaux-de-Fond; on y produit les « copeaux » qui sont assemblés et parfois terminés dans le Canton de Genève.

Mais Roger Dubuis va bien plus loin dans l’appartenance au terroir Genevois: 95% des composants sont produits au rez-de-chaussée du bâtiment de Meyrin. Les seuls éléments produits à l’extérieur sont les rubis, les verres saphir et les boitiers en titane, dont l’usinage entraîne des risques d'incendie difficiles à gérer dans une manufacture généraliste.
Une conséquence imprévisible lors de sa création en 1995, c’est qu'il s'agit sans doute de la marque pouvant revendiquer les plus faibles émissions de CO2 par montre produite: en effet, chaque pièce étant transformée et finie dans le même bâtiment, on évite les sempiternels allers-retours entre les divers sous-traitants.
Si l’entreprise a été crée en 1995, elle ne s'est octroyé le titre de Manufacture qu'au début des années 2000. La démarche désuète et même chevaleresque (la ligne Excalibur s’en trouve légitimée), a consisté à intégrer toutes les étapes de la création d’une montre avant de se prétendre manufacture. A Genève, on est habituellement plus rapide : pour s’auto-certifier "Manufacture", on attend en général de faire les kits presse in-house.
Une fois que chaque atelier était fonctionnel, il se développait horizontalement pour répondre aux commandes. Quand on connait le développement habituel des manufactures Suisses, qui se fait de manière beaucoup plus opportuniste, on peut être étonné par les choix de Roger Dubuis. Mais l’horloger, à l’époque accompagné de Carlos Dias, avait une réelle vision industrielle et horlogère, le choix de construire les fondations avant les murs étant d'une logique imparable.

A titre personnel, je connaissais déjà des manufactures de faible volume (RD produit actuellement moins de 5000 montres par an) fortement intégrées, comme De Béthune… Mais le niveau d’intégration de la production Roger Dubuis, avec le Poinçon de Genève, est un fait unique. Et l’obsession du In-house va très loin, car du plus rare composant, le spiral, au plus commun, la vis, tout est transformé et fini en interne.

Le plus surprenant, lorsque vous arrivez au RDC de l’immeuble de Meyrin, c’est que vous tombez nez à nez avec des machines à décolleter. Alors certes, au premier abord, une décolleteuse n’est pas très sexy (en tous cas beaucoup moins que certaines finisseuses). Mais d’habitude, même les manufactures les plus prestigieuses délèguent la production des vis à des maisons comme Affolter… Le décolletage est plus connu pour sa production de roues. C’est un excellent moyen d’obtenir un maximum de réactivité lors de la production de ce type de composant, afin d'optimiser les côtes en vue du polissage ultérieur, par exemple.

Les roues, pignons et vis vont subir un travail de finition (quasiment toujours du polissage) systématique. Dans les divers ateliers, chaque finisseur est spécialisé dans une catégorie de pièces.
Pour finir les dents de roue, par exemple, on emploie des disques faits de divers type de bois, poirier, hêtre, buis… La « meule » est légèrement décalée avec une pièce de bois (en général un cure dent), afin d’obtenir le mouvement excentrique d'une vis sans fin et de passer successivement entre les dents de chaque roue; Le type de bois et l’épaisseur du « décaleur » sont conditionnés par le type de roues à polir. Dans ce genre d’opérations, ce sont moins les temps de polissage (entre 3 et 15 sec.) qui sont longs, que les opérations intermédiaires de protection et de rangement des roues.
Ainsi, les pignons sont produits dans l'atelier mitoyen. Par exemple, un pignon de roue requiert 17 opérations de polissage différentes, affectées à un même opérateur. Celui-ci doit donc changer de machine autant de fois que nécessaire, en faisant tous les réglages appropriés à chaque étape.
Vu la minuscule échelle des composants en question, c’est un travail de fourmi, au sens propre.

L’autre grande activité du rez-de-chaussée de la Manufacture Roger Dubuis, c’est la découpe et la finition des ponts et platines.
Les opérations de découpe sont assez courantes et sont en général effectuées sur des blocs de laiton.
L’une des spécialités Roger Dubuis, ce sont les magnifiques squelettes, notamment celui du double tourbillon à différentiel. Chez RD, les squelettes conçus comme tels quels dès le départ, sont réalisés directement à la commande numérique; ainsi, toutes les contraintes d'usinage sont calculées d’emblée, ce qui évite la déformation des fragiles platines.
Dans un but similaire, les décorations de ces derniers sont effectuées à la machine, notamment à la guillocheuse numérique; en effet, les machines sont plus constantes dans leurs mouvements et plus économes en termes de matériau retiré, une qualité précieuse pour la stabilité d’une pièce squelettée.

Quant aux ponts et platines classiques, ils passent systématiquement par l’atelier dit « Poinçon de Genève ». C’est l'un des départements les plus actifs de la Manufacture: plusieurs dizaines de finisseurs s’affairent à rendre beaux tous les composants du mouvement. Les techniques sont assez classiques, guillochage, cote de Genève, polissage (avec des disques en "dessous de chope de bière"). La recherche obsessionnelle de la bienfacture et son application systématique sont toujours aussi impressionnantes.

La dernière partie notable au rez-de-chaussée, c’est l’atelier de prototypage. Les horlogers-prototypistes ont toute latitude pour appliquer les plans des concepteurs, avec plusieurs commandes numériques indépendantes ainsi que toutes les machines nécessaire au finissage et à l’assemblage de base; ils sont totalement indépendants en ce qui concerne la fabrication des prototypes. Ainsi, l’activité générale n’est pas impactée, la réactivité et la confidentialité sont maximums.

Ensuite, nous avons la chance de visiter le cœur de la Manufacture (métaphoriquement et physiquement: l’atelier est logé au centre même du bâtiment), lorsque nous entrons dans l’atelier où l’on fabrique et l'on assemble les blocs d’échappement. Malheureusement, la porte de l’atelier qui transforme les blocs d’Elinvar en spiraux nous restera fermée.
Néanmoins, les horlogers qui assemblent les blocs d’échappement nous confierons quelques secrets.
Aujourd’hui, Roger Dubuis utilise deux familles de spiraux: les petits, pour les mouvements à 28800 a/h, et les gros à 21600 a/h, pour les tourbillons. L’assemblage du bloc d’échappement est l’opération la plus stratégique dans le processus de fabrication d’une montre chez Roger Dubuis. En effet, chaque pointage est modulaire et permet l’assemblage et le démontage du bloc d’échappement en une seule opération très aisée.
Tout le délicat travail de réglage s’effectue donc dans cet atelier. Les techniciens sont qualifiés au-delà du concevable et la communication avec l’atelier de transformations des Spiraux ne peut être plus directe, une seul porte les séparant.
La demi-douzaine de techniciens assemble seulement 25 blocs par jours, soit deux heures en moyenne par bloc. Tout d’abord, les spiraux sont coupés et sertis à la virole; on y ajoute ensuite le balancier et les autres composants. Un bloc d’échappement de tourbillon comprend environ 60 éléments…

Cet énorme travail en amont est payant, car il facilite grandement le travail des horlogers et du SAV. Pour des résultats de ce type :
Excalibur Tourbillon volant :

Excalibur double tourbillon volant :

Monégasque Tourbillon :
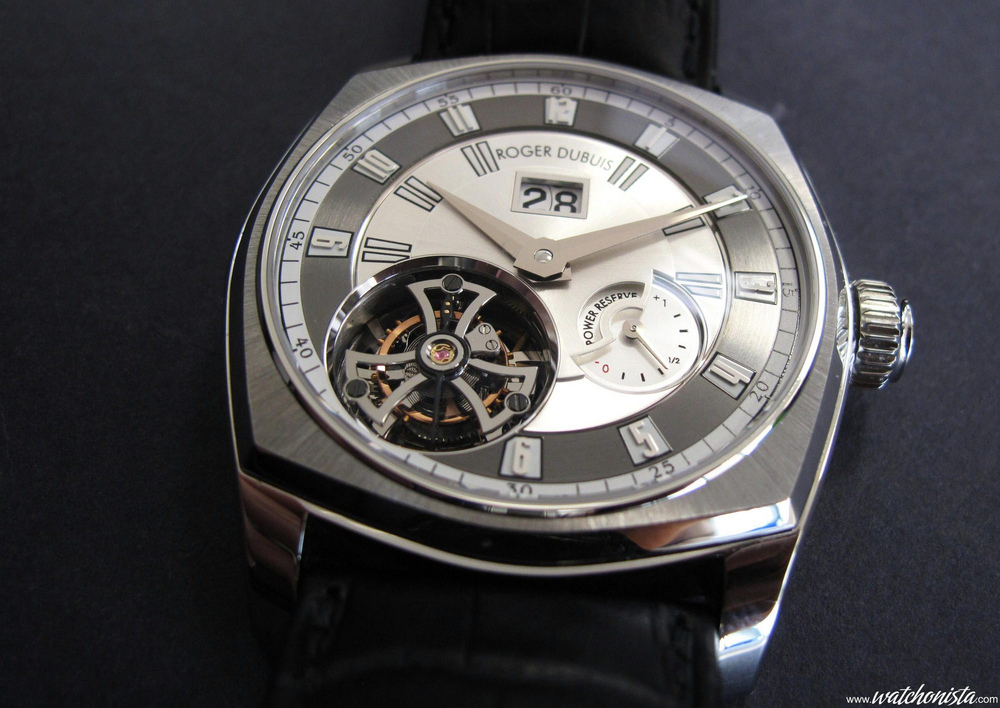
Excalibur 42 :

Velvet :

Pulsion Chronographe :

Monégasque Club :

Au cours des nombreuses visites de manufactures que j’ai effectuées ces dernières années, je n’avais jamais constaté une telle démonstration de force, un tel acharnement qualitatif. Si certaines très belles maisons possèdent autant de savoir-faire (mais pas plus), ces compétences sont le plus souvent dispersées sur plusieurs communes. Ici, c’est hallucinant: un seul site, Genevois de surcroît, concentre la quasi-intégralité des métiers et des machines nécessaires à la fabrication d’une montre de haute horlogerie. Finalement, le Poinçon de Genève intégral n’est qu’une conséquence.
Aucun commentaire:
Enregistrer un commentaire